How to Create Catalogue Products
Once your materials and services are set up in your catalogue, you can create products, which are combinations of parts and labour that allow you to quote more quickly and accurately.
In this article:
Part Types and Measurements Explained
Restricting Product Parts to Style Options
Editing Existing Products in Quotes
Adding Product Presets to a Quote (external article)
Creating Product Components (external article)
Why should I create products?
- Having a 'core range' of complete products set up will significantly reduce the amount of time you spend on quoting.
- Products can be created with parametric parts and style items, meaning you can change the product dimensions or material options with one click, and your quote will recalculate the cost for you automatically.
- Products also include labour durations for key manufacturing operations. This will improve the accuracy of your quoting, because your quotes will include materials costs and labour costs.
- Once your customer accepts the quote and a job is created, your products - including materials and labour time - will be transferred to the job, saving you time on data entry and keeping key information accessible to your staff.
Accessing Your Products
To access your products, navigate to Catalogue from the User Menu Panel on the left, then click Products at the top of the screen:
Creating a Product
To create a new product, follow these steps:
- Go to Catalogue > Products, then click Create.
- Name your product.
- Enter the SKU/Product Code if you have one.
- Enter the Barcode if required.
- Choose a Product Type (e.g. "Base Cabinet", "Counter Top").
- Add your product Dimensions if known.
- Choose a Pricing Strategy (see below).
- Click Create again.
You'll be redirected to a summary page showing your product information.
Examples:
Tip: When entering product dimensions, use the most common size your product is made in. You can always adjust dimensions for individual products inside a quote.
Pricing Strategy: Fixed Pricing vs Variable Pricing
Fixed Pricing: Allows you to set a required sell price for this product, which will be applied automatically when you add the product to a quote.
Variable Pricing: We recommended choosing Variable Pricing if assigning parts or components to your products. This will mean that when linked materials or components are updated (including pricing), your products will be updated also.
Adding Parts to a Product
Once you've created a product, it's time to add product parts. You can do this by following these steps:
Click Add a new part:
- Choose a part Type (see Part Types Explained).
- Fill in any other details for your part (this will depend on the Type).
- Click Create.
You will be taken back to the product summary, where you will now see your part added. You can click into the Name, Quantity or Type fields to edit the part further.
Repeat steps 1-4 until you have added all your parts.
Part Types and Measurements Explained:
- Item: Manually enter an item and a fixed price for a part of your product that is not set up in your catalogue.
Proportional Item: Add a required material and then apply a parametric measurement for selected properties for this item (e.g. length, width, depth, volume, or weight).
The pricing of the proportional item will then change according to the material price multiplied by the part size when you add your product to a quote.
Style Item: Use for parts that have more than one range option. For example, the product might be a drawer, and the style item might be "handles". You might use cheaper or more expensive handles across different quotes. Setting the handle as a style item allows you to easily select the option you want for each quote.
Some style items are also proportional (for example, benchtops), and will require parametric measurements.
- Material: Add a specific material from your catalogue.
- Labour: Add the operation(s) required to manufacture this product, enter the duration, and click Create. Once the labour is added as a part, your quote price will adjust based on the product size and required labour time.
Service: Add a service that may be required from an external provider, such as painting, cleaning, delivery, etc.
Part Dimensions Explained:
Please note: It is essential to add your labour as a product part, because this allows you to assign the product against the required operation once your quote is accepted and turned into a job.
![]() |
![]() |
![]() |
![]() |
Restricting Product Parts to Style Options
You can set up product parts that only get added to quotes when specific style options are applied to the product.
For example, let's say you have a product that requires 20 minutes of the operation "Painting". You can create a labour part, and the labour will be factored into the cost when the product is added to a quote. However, you may only need to paint this particular product when certain conditions are met, such as when a specific material is used.
To prevent this 20 minutes of labour being incorporated into the product's cost when it's not necessary, you can "restrict" the part to only apply if one of the style options "Category A Paint" or "Category B Paint" are selected.
To restrict a part to style options, simply create (or edit an existing) part and change Restrict to Style Options from All to Selected, then choose the relevant style options you want the part to be applied to.
When you add this product to a quote, by default this part will not be displayed or included in the calculations for the product, unless one of the style options has been applied.
Note: When viewing a product in your catalogue, the calculated values (cost/overhead/wastage etc.) will only include parts with Restrict to Style Options set to "All." This means that products with style options selected may be significantly more expensive in a quote than in your catalogue listing.
Additionally, if you don't want a part to be added to a quote in any circumstance, you can change "Restrict to Style Options" to "None". This can be useful for creating "Draft" parts.
Style option restrictions can also be applied to Product Components. Find out more
Updating a Product Part
To update an existing part, simply click on the part name inside your product. An Edit window will open, into which you can enter any changes required. Click Save Changes to finish.
Copying Products
Use the Copy function when you need to set up two or more similar products, rather than having to create them again from scratch.
Simply click into the product you want to copy, click the three-dot menu at the top left, then click Copy:
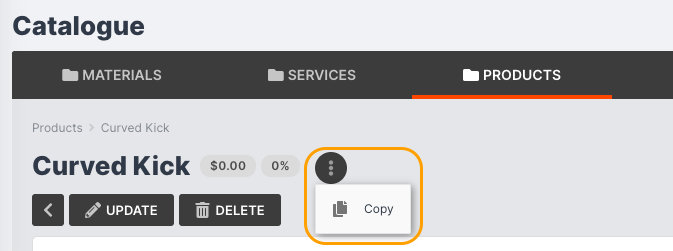
A pop-up will appear and ask you to confirm. Click Copy again, and you will be redirected to your new product summary, where you can add or remove parts or make any other changes needed.
Tip: Your new product will be called "[Product Name] Copy", so that you know you are editing the correct product. Edit the name at any time by clicking Update.
Editing Existing Products in Quotes
Once you've created a quote and added your products, you can update these on the fly for any client who wants to make changes from your standard set-up. This will not edit the product as it appears in your catalogue - only the specific product used in the quote.
To edit a product inside a quote, follow these steps:
- From the User Menu Panel, go to Quotes.
- Click into the quote you want to edit, and click Update.
Click into the product you want to edit (see below):
Editing Products in Quotes Inside the product, you can:
- Edit an existing part by clicking into it and making changes.
- Copy or delete an existing part by selecting it with the checkbox and using With Selected.
- Add a new part by clicking Add New and selecting the part Type from the drop-down.
- Click Save Changes.
Adding Product Presets to a Quote
See: Creating Quote Presets with Products
Creating Product Components
See: How to Create Product Components